A journey through Novotema: the sealing solution’s design
Our strength lies in knowing exactly how to support the customer during every stage of the production process, starting from the design of the sealing solution.
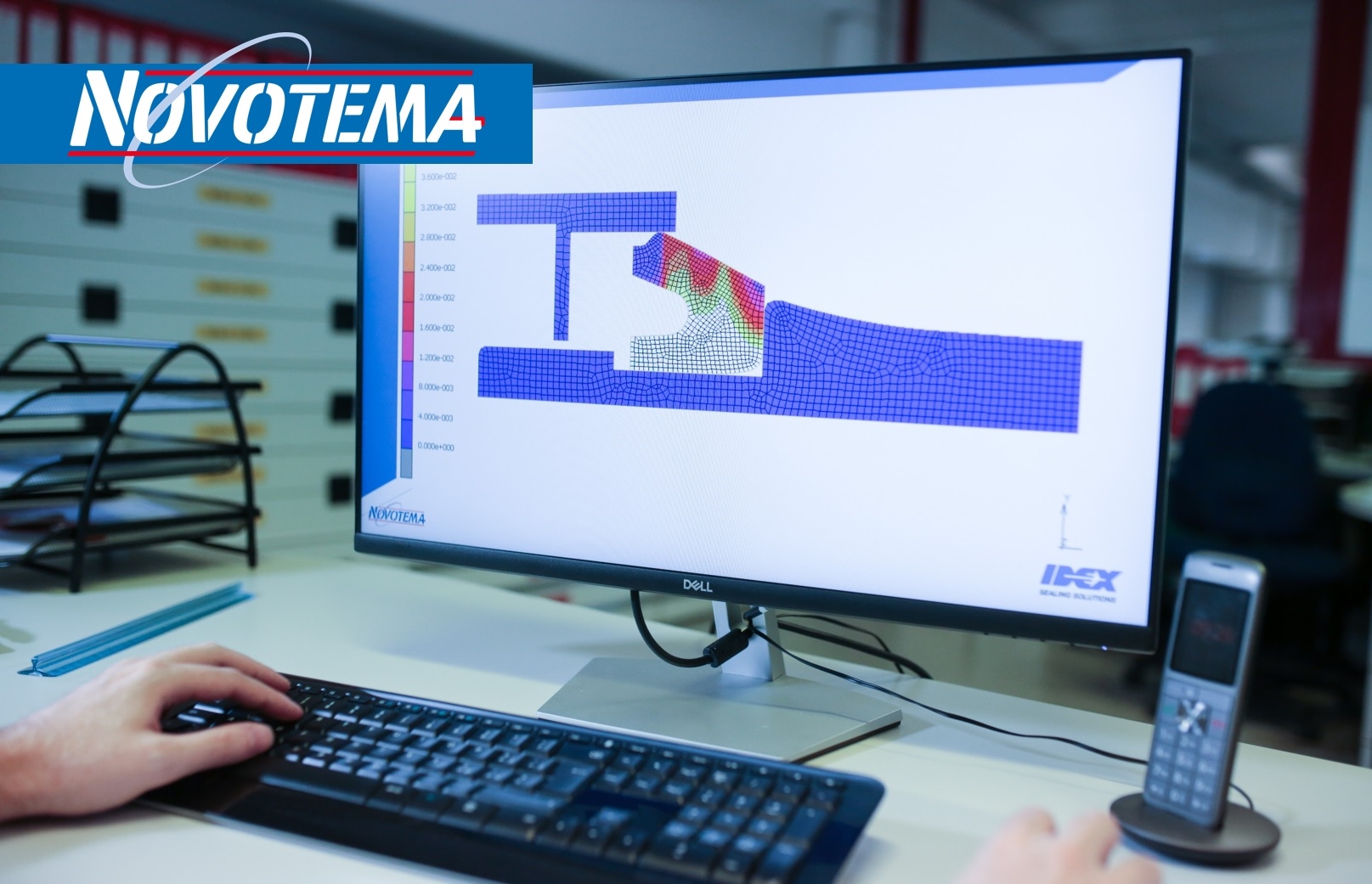
Our strength lies in knowing exactly how to support the customer during every stage of the production process, starting from the design of the sealing solution.
When a customer gets in touch with us, there are few typical scenarios.
There is the case where the customer already has an idea about the design of the sealing solution for its project and he needs to confront with us to verify its effectiveness or to work with us on an optimization.
Or it can happen that the customer already has a sealing solution but it does not work properly and does not meet the operating requirements. In this case, a deep problem analysis and a fine tuning of the sealing solution’s design are required.
Finally, it might be the case that the customer has no experience in gaskets development and therefore needs to start the design of the sealing solution starting from scratch.
Novotema is able to manage each one of these cases, working on the co-design of the gasket together with the customer.
Why are we talking about co-design?
This term is used to precisely define the design phase of the sealing solution which sees the active cooperation of our technical department together with the customer's technical office.
This extremely important teamwork and the constant exchange of information, for example on the type of performance required, on the application and on the various parameters that are involved, create the conditions to design the most suitable sealing solution for the customer's specifications. The customer will then have to test the sealing solution on its side and validate the project.
Now let's get into a little more detail on how a gasket is designed.
First of all, we must take into consideration whether the customer requires a static or dynamic sealing solution. Furthermore, all the details and technical specifications of the project must be examined, such as, for example, the pressure and temperature ranges to which the gasket will be subjected, any deformations and friction forces involved, external contact agents, etc.
This will allow our technical department to make hypothesis on the material to be used and on the geometry of the gasket.
The material will be characterized and the data will be entered into a peculiar advanced structural simulation software (Marc Mentat MSC) thanks to which we will be able to simulate the behavior of the sealing solution in operation so that we can pursue the best performance possible.
The following step is to create a prototype mold that allows us to print samples in order to test the application in operation.
Once the customer has validated the geometry, the material and the performance in accordance to the project specifications, we will then move on to the next phase, such as the series mold.